The circular economy concept aims to break free from a throwaway business model into one that fosters the extended life of resources through reclamation and recycling after consumption. When executed effectively, every step of the process (design, manufacturing, use, collection, and reprocessing) contributes to a singular goal to keep parts and materials within the economy for as long as possible.
This is very difficult to execute, mainly because there are no real incentives for consumers or manufacturers to recycle and/or reclaim materials at the end of a product’s life. It’s often much easier and less expensive to put durable goods into the trash.
Thanks to new initiatives underway by The National Institute of Standards and Technology (NIST) , there’s guidance on the horizon to help manufacturers sort out the challenges of institutional recycling and reclaiming. Plus, we can learn from other industries adopting broad recycling methods that are proving it to be a smart, cost-saving business imperative.
Creating a system
So how does a manufacturer go about the process of recycling and reclaiming resources at the end of a product’s life? NIST is working to address that challenge by developing circular economy standards.
“We don't have good systems for reclamation right now, and it’s challenging to put those systems in place because it's not the responsibility of just one person or one job category,” says KC Morris, Life Cycle Engineering Group leader at NIST. “We can envision a system in the future that has identifiers built into parts as a product is being manufactured so that at the end of a product’s life, those parts can more easily identified for sorting to be reused, recycled, or thrown away.”
In a product take-back approach, there are a few models to explore, such as refurbishing products and reselling them, disassembling products and reusing their components, or recycling the components that get processed into raw materials used to make other products. Started in 2022, NIST has been developing two related projects:
The Closed-Loop Recovery Project is exploring end-of-use recovery for high-demand consumables, with an emphasis on two problem areas: plastics and solar photovoltaics. The goal is to develop a model to inform decision making when planning for recovery by including processing methods and logistical needs, along with economic and environmental considerations. Ultimately, the approach could be applied to a range of durable products.
The Circular Product Design Project is studying different product design methods that give design engineers better insight into considerations for material availability and variability, end-of-use options, environmental impacts of the manufacturing, and alternative business models, such as remanufacturing. These findings are captured in an in-progress standard on Principles for Circular Product Design from ASTM International’s E60 Committee on Sustainability.
Morris cites the ink cartridge remanufacturing industry as a great success story for the circular economy model. Recycling ink cartridges is simple because there are convenient collection sites at office supply stores, electronics stores, and other large retail locations. Many toner manufacturers and some online remanufacturers offer an incentive for sending them empty cartridges. A 2023 report from Consegic Business Intelligence predicts that the printer ink cartridge market will reach more than $22.9 billion by 2030.
Streamlining Product Materials for Efficiency
The barriers to higher rates of recycling and reclamation are often related to the materials specified in the product design process.
“Product engineers can make recycling easier by minimizing material variety in manufactured products, adopting modular product designs, and avoiding material alloying elements that make recycling more challenging,” says John Sutherland, head of Environmental and Ecological Engineering at Purdue University.
Changes in product demand are another recycling challenge. Sutherland states that end-of-life products (he prefers avoiding the word “scrap” since this sets the tone for how a used product is valued) may contain a mix of materials that reflect the composition of production from previous years and product models. These material compositions may not align with the current material mix.
For example, the automotive industry requires an increasing proportion of aluminum relative to ferrous alloys in vehicles; this is at odds with the used material stream that contains a much higher ferrous content. This mismatch tends to lower the economic value of the recycling stream. Moreover, energy- and carbon-intensive virgin metals are then needed to produce new vehicles.
According to a report from The REMADE Institute, 700 commercial aircraft retire annually, and each plane is made of 80% aluminum by weight, so decommissioned aircraft are a valuable material resource.
REMADE partnered with a team from the University of Illinois at Urbana-Champaign and Eck Industries (a producer of aluminum mold castings) to develop a new process for recycling wrought aluminum alloy that converts airplane scrap directly into a high-strength, castable secondary alloy with mechanical properties comparable to premium aluminum casting alloys.
It Takes a Village
The construction industry is taking steps toward improving its reuse policies. Following an increasing number of old residential demolitions in the area, the city of San Antonio, Texas, adopted a deconstruction ordinance in September 2022 that requires older housing stock to be deconstructed instead of demolished. This prompted the start of a program called San Antonio Reuse, which is managed by the San Antonio Office of Historic Preservation (OHP).
“We’re using an organ donor analogy,” says Stephanie Phillips, program manager of Deconstruction & Circular Economy at the OHP. “Parts of a building may have reached the end of their life, but they can be reused to help extend the lives of dozens of other structures.”
The program has repurposed a historic village that was the site of a decommissioned Air Force base for the Material Innovation Center — complete with a reclaimed material warehouse, hands-on training for tradespeople, public workshops, and a community tool library. The warehouse collects donations such as lumber, siding, doors, and windows. Those materials are cycled back into the community through affordable housing programs.
The village hopes one day to expand into reclaiming other materials such as electronics, textiles, and manufacturing materials.
Urban Machine has developed an automated system to detect and remove metal fasteners from used lumber so it can be reused as premium building material.
Automated Reclamation
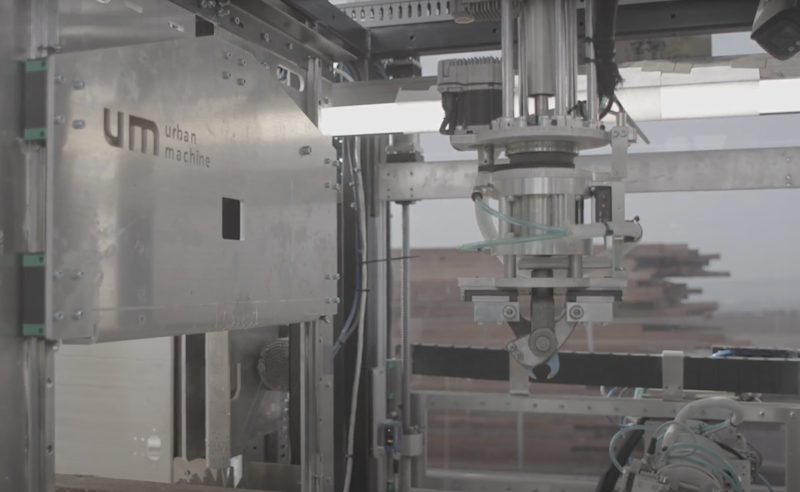
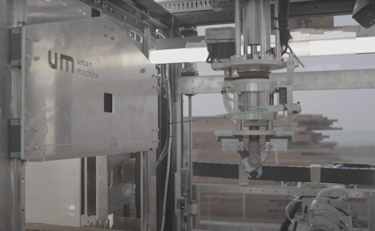
A robotics company has turned the task of reclaiming wood waste from construction and demolition into a business called Urban Machine. An automated system turns wood otherwise destined for landfills into valuable, reusable lumber.
When previously used wood is fed into the machine, a 3D vision system identifies metal fasteners such as nails, screws, and staples, and removes them with a 3-axis robot that was custom-designed at Urban Machine. As a final quality control measure, the lumber is run through a Fortress Technology metal detector, ensuring that it is metal-free and ready to be reused again as a premium building material. The machine can travel via trailer to be used at a construction site, lumber yard, or recycling facility.
The old growth wood is highly sought after by furniture makers and construction companies because it is harder and stronger than virgin lumber found in lumber yards today. By automating the process, Urban Machine is able to keep the cost of reclaimed lumber about the same as virgin. More architects are specifying reclaimed lumber in the design, so Urban Machine has provided a unique opportunity to share the wood’s provenance.
“We stamp a QR code onto our wood to share its history,” says Jorie Wisnefski, marketing manager at Urban Machine. “It's interesting to learn the story, for example, that a beam came from the deconstruction of an old school gym and when the gym was first built.”
Plastic to Carbon
Researchers at the University of Southern Mississippi’s Polymer Science and Engineering Department have been studying plastic recycling and converting plastic waste materials into functional and value-added products.
They are investigating a method to convert waste polypropylene (a common polymer) into feedstock that can be 3D printed into carbon-based structures that are very durable. This process would not only capture carbon from polymers so it doesn’t become an environmental pollutant, but it could also be used to make carbon structures used in environmental remediation such as oil absorption, chemical synthesis, or plastic deconstruction.
The technology is now ready for commercialization and scale-up, so we may see this new plastic recycling method being used in the next couple years.
“We need to think about waste materials as resources that have the potential for infinite life,” says Zhe Qiang, assistant professor USM’s Polymer Science and Engineering Department. “It’s not enough to think of products as just being recycled. We need to consider the energy used and carbon emissions for developing those recycled products.”
Qiang is vice chair of TC 4 – Recycling of Composites Technical Committee for the Society for the Advancement of Material and Process Engineering. Involving societies and other organizations within the industry is an important step in developing a more holistic recycling solution. If you’re interested in joining SAMPE’s Recycling of Composites Technical Committee, visit their website.
These examples show promising potential for government agencies, manufacturing companies, and trade associations to work together to develop recycling and reclamation programs for materials and components. In addition to a positive environmental impact, we can conserve resources and reduce costs over time.
Learn more about the importance of choosing more longer-lasting materials and responsibly-sourced materials in MY previous article, “Greener Manufacturing: Sourcing Materials More Responsibly.”
Want inspiration? Check out the newest advanced materials and processes at IMTS 2024, held Sept. 9-14, 2024, at McCormick Place in Chicago.